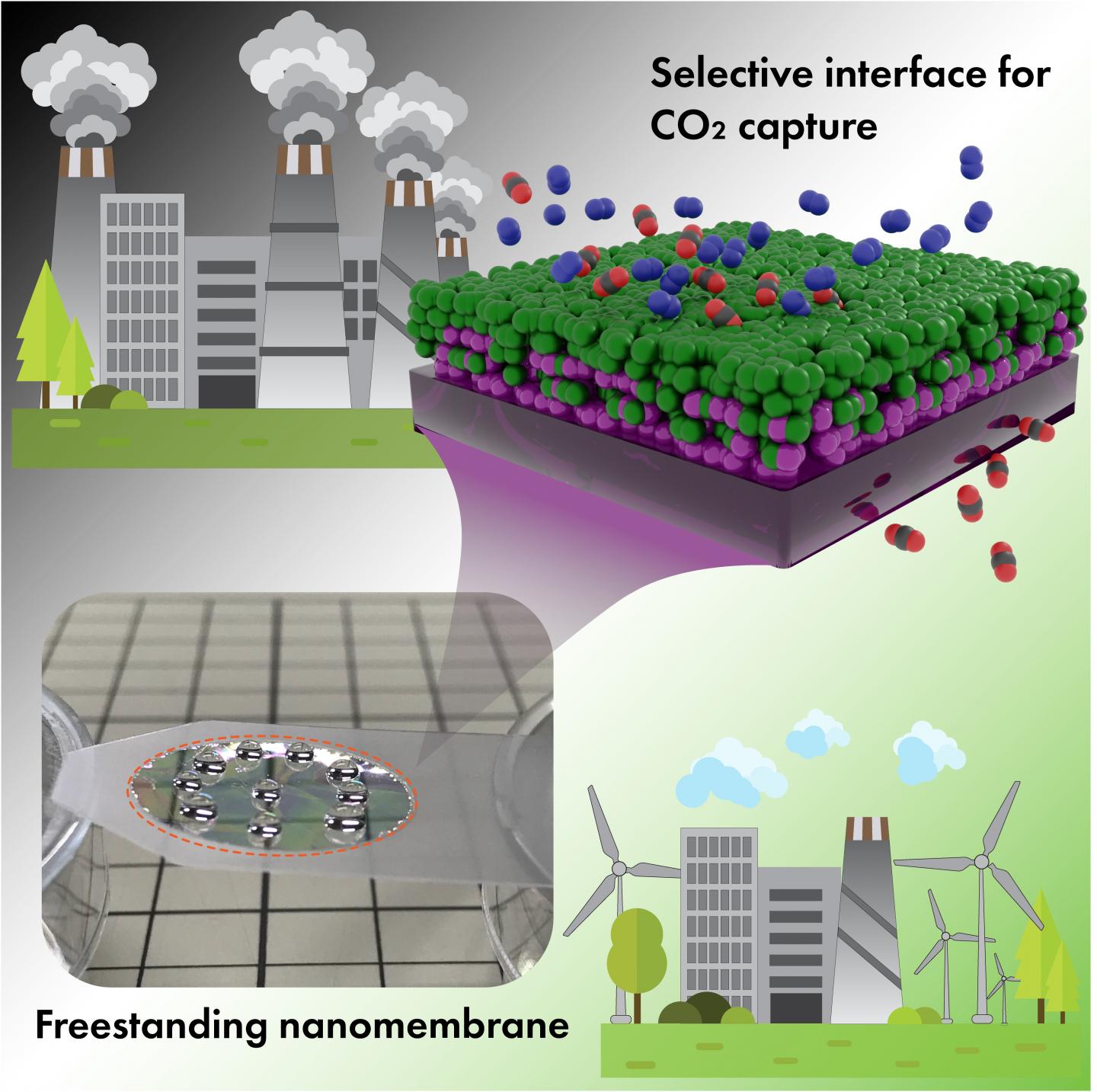
IMAGE: Freestanding and mechanically strong nanomembranes composed of two polymeric layers demonstrated superior carbon dioxide separation from nitrogen. As revealed by the study the surface of the composite membrane played a…
view more
Credit: Roman Selyanchyn, I2CNER, Kyushu university
Climate breakdown caused by the emissions of carbon dioxide (CO2) into the atmosphere is a major existential problem faced by humanity right now. The most acceptable solution would be complete termination of the use of fossil fuels or at least fast reduction of their use by all countries, in line with the Paris agreement. This will ensure the planetary warming is limited by 2 C. The emissions reductions, however, are slow and most of the countries are unlikely to reach the goals of reduction.
Technological solutions for the massive CO2 emissions prevention are therefore critically needed. Some technologies for CO2 capture, for instance, sorption by liquid amine chemicals are already mature to be applied on a scale, however they are costly and come with a burden of toxic chemicals disposal once they lost their CO2 binding property. Alternative technologies are therefore of a great importance.
Separation of gases with the help of membranes is emerging as a key technology for the establishment of a sustainable energy society. Wide deployment of membranes can help to capture huge amounts carbon dioxide emitted in the variety of industrial processes. In contrast to conventional CO2 capture, gas separation with membranes provides a promise for cost-efficient solution. However, to achieve economical CO2 capture at mass scale the membranes need several critical features: fast CO2 transport through their structure; high CO2 selectivity (i.e. to be a less permeable barrier for other gases); mechanical strength and chemical resistance. Additionally, membranes should be composed of materials that are inexpensive at mass production, and this is the reason why organic polymers, (conventional plastics and rubbers) are most attractive for industrial applications.
Thin-film composite is a specific architecture of the membranes to provide the robust structure for industrial applications. These membranes, that contain multiple functional layers (made of organic polymers) in its structure, offer a good solution for large-scale CO2 capture. However, even benchmark organic polymers with best separation performance (high CO2 permeability and high CO2/N2 selectivity) are struggling to deliver satisfactory separation performance, because of inability to form sufficiently thin, defect free and mechanically stable membranes.
In this work we report for the first time how ultimately thin selective layers (thickness of several nanometers) can be used to achieve desired separation properties. We have used well-known polymers for this study: polyether block amide (Pebax-1657) as selective layer and polydimethylsiloxane (PDMS) as gutter layer and examined what happens with the gas separation property when thickness of the selective layer pushed to the extreme of several nanometers. We have discovered that when selective layer of separation membranes becomes very thin it can form specific interface with gutter layer in composite structure. This nanoscale interface delivered unexpectedly high selectivity towards CO2. Gentle and ultra-short plasma treatment of the hydrophobic PDMS layer that is needed to promote adhesion with hydrophilic selective layer revealed itself as a tool to control and tune the “activity” of the molecular interface between two polymers.
We found that this interface made a determining impact on the membranes CO2 selectivity. Together with high permeation rates enabled by low thickness, developed membranes fit nicely into the area of the separation properties needed for industrial CO2 capture (e.g. post-combustion capture at fossil fueled power plants). These results open a new unexplored area of the interface-governed gas separation that can be used by engineers to design more efficient membranes for variety of useful applications.
###
For more information about this research, see “Critical role of the molecular interface in double-layered Pebax-1657/PDMS nanomembranes on highly efficient CO2/N2 gas separation” Olena Selyanchyn, Roman Selyanchyn, and Shigenori Fujikawa, ACS Applied Materials and Interfaces (2020), https:/
TDnews