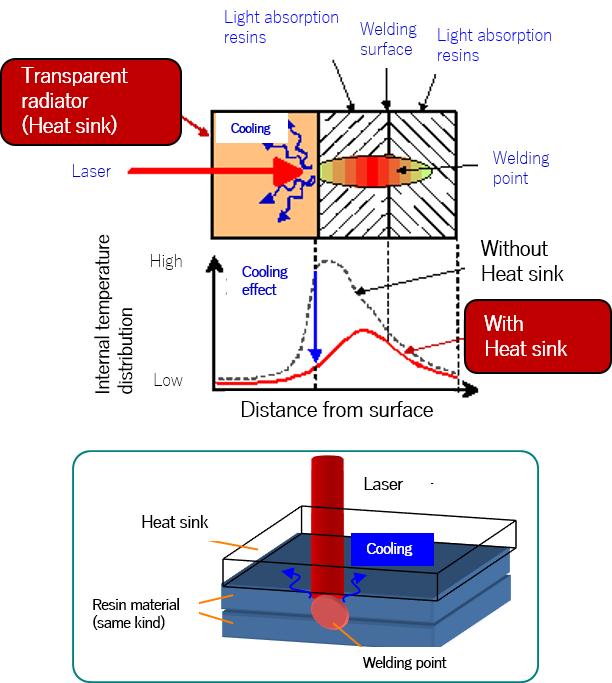
IMAGE: Heat sink laser resin welding principle
view more
Credit: SEIWA OPTICAL CO., LTD.
JST announced the result of the development project “a precision joining device with heat sink laser welding” by Adaptable and Seamless Technology Transfer Program through Target-driven R & D (A-STEP) enterprise-led phase NexTEP-A type as successful. We have commissioned SEIWA OPTICAL CO., LTD., for practical development of a precision joining device for electronic devices through heat sink laser welding based on the research results of associate professor Kimitoshi Sato of Kokushikan University (specially appointed associate professor of The University of Electro-Communications, Center for Industrial and Governmental Relations at the time of development) and others.
Methods for laminating and sealing resins include welding, which melts the joining faces, in addition to adhesives. Traditional methods of welding include hot-plate/hot-air welding and ultrasonic welding; however, precise heating of the joining faces is difficult, which makes these methods not easily applicable to small parts. For products where burning or vaporization of parts due to excessive heating is problematic, quality assurance of welded product was a major issue.
In this development, a new technique that accurately welds only the joint was put into actual use. This technique uses a laser as a heat source and pressure-welds a radiator that transmits light (heat sink) to a tip of the outlet of the laser while in contact with the surface of the part to be welded. This prevents temperature increase in the surface and the inside of the part (Fig.1).
As a result, we successfully completed a welding device for three types of target parts. For small electrical parts, spot-scanning laser welds irregular outline of PPS (polyphenylene sulfide)(1) while avoiding terminals and the like. For microchannel, spot-scanning laser accurately welds outline of the flow path of COP (cycloolefin polymer)(2) without burning or vaporization (Fig.2). For flat panel, shaped laser beam is sequentially irradiated to seal the whole PET (polyethylene terephthalate)(3) material (Fig.3).
By cooling the resin with heat sink, it was made possible to weld together olefin-based resin and fluorine-based resin that were difficult to weld because of high laser absorption and heat generation. The developed technique is anticipated to contribute greatly to improved appearance and accuracy of the finish, and welding and assembly of precision devices, such as resin casing, medical microchip, and LCD panels, for which reliability is a requirement.
###
(1) PPS (polyphenylene sulfide)
It is a thermoplastic resin with characteristics, such as high heat resistance and rigidity, and used for injection molding, textile processing, and film molding.
(2) COP (cycloolefin polymer)
It is a highly transparent thermoplastic resin with low water absorption, and is mainly used for optics and medical fields.
(3) PET (polyethylene terephthalate)
It is a thermoplastic resin used for films, plastic bottles, and fleece clothing.
TDnews